The prime plate hits the underside plate with a speed of 100–one thousand ms −1 , and pressures are in the range of 10 to a hundred kbar. Under sure situations a superheated layer of material varieties in the contact space.
Most of the metal cladding for the constructing trade is pre-painted in coil prior to the manufacturing of the cladding panels. Metal cladding is used for each safety from environmental factors and aesthetics of the constructing. The paint utilized by coil coating provides the metal more sturdiness, corrosion resistance and final look. Arconic argued that the tragedy at Grenfell was not the result of its panels, however the combination of materials used within the 2016 £10m refurbishment, singling out the plastic window frames through which the fireplace was believed to have first unfold from flat sixteen into the cladding system.
tube. Energy, from fission, is generated approximately uniformly throughout the fuel pellets. Heat is extracted on the rod surface by the coolant circulate. The temperature on the hottest level, on the pellet centerline, is typically in the range 800–1000 °C, relying on the facility stage. The metallic cladding is an efficient conductor, so the temperature rise throughout the wall is just a few tens of degrees.
In December, the government launched new hearth safety regulations in response to Dame Judith Hackitt's impartial review following the Grenfell Tower fire. A public inquiry into the fire, which happened in west London in June 2017, heard evidence to assist the theory that the extremely combustible material within the cladding was the primary cause of the hearth's unfold.
The authorities’s constructing safety programme has targeted totally on instant interim mitigation actions and everlasting substitute of unsafe aluminium composite materials (ACM) panels on high-rise buildings because of the acute dangers posed by such panels.
In addition to metallurgical factors, water chemistry has a strong influence on the corrosion course of in zirconium alloys. The management of water chemistry as required in different reactor systems embrace suitable additions of lithium hydroxide, boric acid, hydrogen/deuterium, oxygen, iron, and zinc. In PWRs, boric acid is added to the coolant water for reactivity control. The pH of the coolant is adjusted by addition of lithium hydroxide which renders the coolant slightly alkaline, to be able to reduce the corrosion charges of structural supplies (stainless steels and Inconels) within the primary warmth transport circuit and thereby inhibit deposition of corrosion merchandise on the gas cladding. Radiolysis of water produces oxidizing species which enhances oxidation rate of zirconium alloys within the radiation environment .
The joint is then brought on by a deformation-induced melting bath. The soften layer is sort of thin; for instance, when cladding an aluminum alloy it's about zero.5–4μm (Kreye 1985, 1997 ). The dilution of the molten zones results in airplane or corrugated interfaces.
In response to this unforeseen consequence, several fixes were introduced. In one, a second inside-floor liner of odd Zry is extruded on the sponge zirconium liner to be able to restore corrosion resistance.
These frameworks have been utilized and peer reviewed inside the scope of fireside research studies on the hearth efficiency of aluminium composite panels and insulation supplies at The University of Queensland and the University of Edinburgh. This giant scale take a look at, undertaken by the Fire Protection Association (FPA), examined a HPL panel system with stone wool insulation, in accordance with British Standard 8414. This check includes building a 9-metre high wall with a complete cladding system mounted to it - together with panels and insulation. This was then subjected to a fire designed to copy the circumstances in which a severe fire breaks out of a window.
Cladding is an outer layer of both vertical or horizontal material, used to improve the appearance, thermal insulation and the climate resistance of a building. Our cladding is available in quite a lot of sizes, forms of timber and floor finishes. Enhance the curb attraction of your house with B&Q cladding. All of our timber is responsibly sourced forest friendly timber. Once the pellet/clad hole is closed, any change in pellet dimensions causes stress in the cladding and the synergy between the stress and the corroding medium induces the SCC course of.
The Building Research Establishment (BRE) has been commissioned to undertake this project. This programme is on-going and exams are expected to conclude in the summer.
Differential swelling between cladding, wrapper tube, and spacing system (spacer wire or grids) can induce extra stresses and deformations on these elements and/or generate coolant circulate perturbations within the bundle. These phenomena have been studied and have significantly shown that wires or grid supplies need to be chosen and specified so as to minimize differential swelling. Laser cladding has been utilized to hardening of steam generator turbine blades and reached pilot manufacturing status [4 ].
Zry comes in two varieties, Zry-2 and Zry-4. These two differ by minor modifications in the concentrations of the transition metals (Zry-4 has no nickel). PWRs use Zry-four whereas BWRs make use of Zry-2 as cladding and either Zry-2 or Zry-4 for the duct or channel holding the gas-factor bundle. The transition metals iron and chromium appear in the microstructure as precipitates of the intermetallic compounds Zr 2 (Ni,Fe) and Zr(Cr,Fe) 2 . These minor alloying components improve corrosion resistance to an extent depending on the scale of the precipitates.

D. Laser Read More Here Cladding

The buildup of those could be suppressed by adding hydrogen within the coolant water. Dissolved hydrogen focus in PWR coolant is maintained at a level of two.2–four.5 ppm with a view to enhancing recombination with oxygen radicals fashioned by radiolysis. The PHWR coolant does not contain boric acid and deuterium is added rather than hydrogen. Dissolved oxygen in PHWR coolant is controlled between 10–50 ppb and it has been noticed that corrosion in each zircaloy-2 and Zr-2.5 Nb pressure tubes rises to an exceptionally high value at high oxygen concentrations.
The government’s constructing safety programme has focused totally on quick interim mitigation actions and everlasting replacement of unsafe aluminium composite material (ACM) panels on excessive-rise buildings due to the acute dangers posed by such panels.
Most of the metal cladding for the constructing trade is pre-painted in coil prior to the manufacturing of the cladding panels. Metal cladding is used for both protection from environmental components and aesthetics of the constructing. The paint applied by coil coating offers the metal extra sturdiness, corrosion resistance and ultimate look. Arconic argued that the tragedy at Grenfell was not the results of its panels, however the mixture of supplies used within the 2016 £10m refurbishment, singling out the plastic window frames via which the fireplace was believed to have first unfold from flat sixteen into the cladding system.
The BWR coolant usually accommodates the next stage of oxygen, usually 200–four hundred ppb. Hydrogen addition in boiling water circumstances is not very effective because of the segregation of hydrogen in the steam phase. The authorities has set up a fund to take away cladding from buildings identified with aluminium composite material (ACM) - the identical sort used on Grenfell Tower. The new checks, which started final month, are testing other kinds of cladding and building materials.
Cladco’s cladding options are also moisture resistant, improving their longevity and minimising the common maintenance required for other cladding choices. The flammability of cladding materials (aluminium composite panels, insulation, and some other materials similar to sarking) is defined based mostly on properly-established testing frameworks extensively accepted within the hearth safety engineering group.
The joint is then brought on by a deformation-induced melting bathtub. The melt layer is sort of skinny; for example, when cladding an aluminum alloy it's about 0.5–fourμm (Kreye 1985, 1997 ). The dilution of the molten zones ends in aircraft or corrugated interfaces.
Phase transformation of Zirconia is, however, of nice concern. Zircaloys additionally undergo from bad creep charges. In contrast to surface-layer welding, explosive welding causes no change in microstructure, and corrosion resistance of the layers isn't affected (Pocalco 1987 ). ions from the setting to the reaction entrance on the metal/oxide boundary.
The interplay that gas cladding tubes expertise because of the fission products on the inside surface is stress corrosion cracking (SCC). Iodine, caesium, and cadmium are a few of the fission products which contribute strongly to the SCC course of.
In response to this unforeseen consequence, several fixes have been launched. In one, a second inner-floor liner of ordinary Zry is extruded on the sponge zirconium liner in order to restore corrosion resistance.
tube. Energy, from fission, is generated approximately uniformly all through the fuel pellets. Heat is extracted on the rod floor by the coolant flow. The temperature at the hottest level, on the pellet centerline, is typically within the vary 800–one thousand °C, depending on the facility degree. The metallic cladding is a good conductor, so the temperature rise across the wall is just a few tens of levels.
The prime plate hits the bottom plate with a speed of one hundred–a thousand ms −1 , and pressures are within the vary of 10 to 100 kbar. Under sure circumstances a superheated layer of material types in the contact space.
Metal is the most vitality-efficient and sustainable constructing materials available. Next to this it's virtually fully recyclable and present steel coils contain a excessive recycling content material up to 95%. The engineering of our materials additionally makes our cladding a powerful resilient form of exterior covering . The bonding agent reinforces the wooden parts, and our additives enhance the cladding’s climate resistance.
The blades had a machined pocket, into which powdered cobalt-based steel (Stellite 6) was fed ahead of the laser beam. The resulting cladding layer was well bonded, and the blades exhibited improved fatigue traits in contrast with blades fashioned by the standard silver brazing course of.
The effect of lack of steel by internal or outer corrosion is less necessary for thick cladding than for thin-walled tubing. For the same exterior loading, the stress produced within the cladding, both external from the coolant or inside from fission-product swelling of the gas, is reduced in proportion to the wall thickness. However, thick cladding is detrimental to neutron economic system, increases the quantity of the reactor core, raises fuel temperature, and costs greater than skinny-walled tubing. The compromise between these competing demands has produced wall thicknesses of ∼0.9mm in BWRs and ∼zero.7mm in PWRs. is produced and the risk of a large secondary hydriding failure is elevated.
D. Laser find this Cladding
tube. Energy, from fission, is generated approximately uniformly throughout the gasoline pellets. Heat is extracted on the rod floor by the coolant flow. The temperature on the hottest point, on the pellet centerline, is typically within the range 800–a thousand °C, relying on the ability degree. The metallic cladding is an efficient conductor, so the temperature rise across the wall is just a few tens of degrees.
In December, the government launched new fireplace safety regulations in response to Dame Judith Hackitt's unbiased review following the Grenfell Tower hearth. A public inquiry into the hearth, which happened in west London in June 2017, heard proof to help the speculation that the highly flamable materials in the cladding was the first reason for the fireplace's spread.
Phase transformation of Zirconia is, however, of nice concern. Zircaloys also suffer from bad creep rates. In distinction to surface-layer welding, explosive welding causes no change in microstructure, and corrosion resistance of the layers just isn't affected (Pocalco 1987 ). ions from the surroundings to the reaction front at the metallic/oxide boundary.
The buildup of those may be suppressed by including hydrogen in the coolant water. Dissolved hydrogen focus in PWR coolant is maintained at a degree of 2.2–four.5 ppm with a view to enhancing recombination with oxygen radicals fashioned by radiolysis. The PHWR coolant does not comprise boric acid and deuterium is added instead of hydrogen. Dissolved oxygen in PHWR coolant is controlled between 10–50 ppb and it has been noticed that corrosion in each zircaloy-2 and Zr-2.5 Nb pressure tubes rises to an exceptionally high value at excessive oxygen concentrations.
The authorities’s building security programme has targeted totally on instant interim mitigation actions and everlasting replacement of unsafe aluminium composite material (ACM) panels on high-rise buildings due to the acute dangers posed by such panels.
Due to the combined results of thermal enlargement of gasoline pellets, gas swelling as a result of fission fuel launch, and the coolant stress on the outer floor of fuel tubes, cladding tubes collapse on the gasoline pellets. In PWRs the closure of the hole between the pellet and the clad takes about one full energy year whereas the gap is maintained for a longer period in BWRs.
In addition to metallurgical elements, water chemistry has a robust affect on the corrosion course of in zirconium alloys. The management of water chemistry as required in several reactor techniques include suitable additions of lithium hydroxide, boric acid, hydrogen/deuterium, oxygen, iron, and zinc. In PWRs, boric acid is added to the coolant water for reactivity control. The pH of the coolant is adjusted by addition of lithium hydroxide which renders the coolant slightly alkaline, to be able to cut back the corrosion rates of structural materials (stainless steels and Inconels) within the primary heat transport circuit and thereby inhibit deposition of corrosion merchandise on the gas cladding. Radiolysis of water produces oxidizing species which enhances oxidation fee of zirconium alloys within the radiation environment .
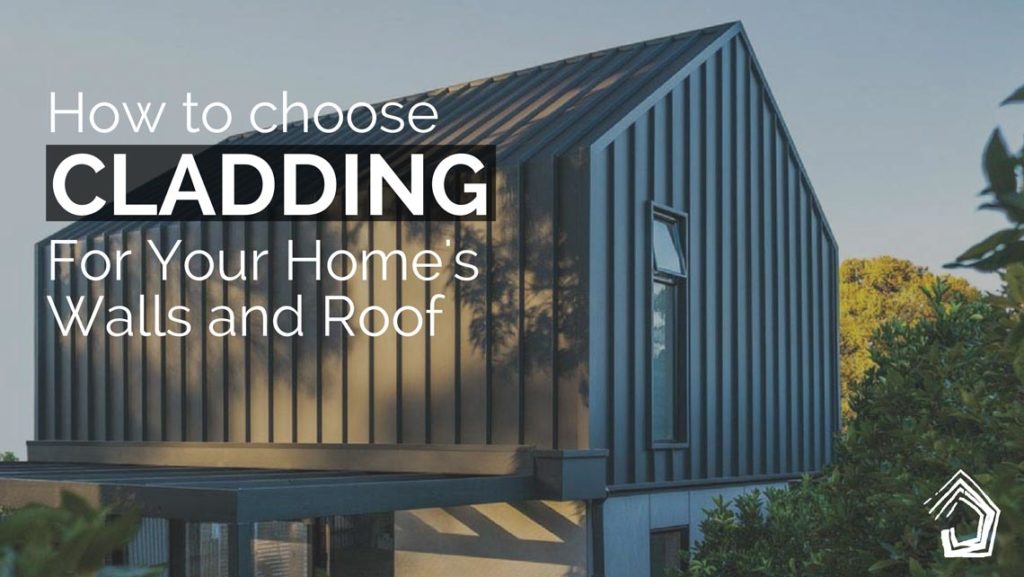
Metal components

The helium filling fuel is also a reasonably good conductor, but solely so long as it remains uncontaminated by fission merchandise. The poorly conducting ceramic gas pellets are responsible for almost all of the temperature rise. The evolution of the conductivities of the pellet and filling gasoline decide how the thermal performance develops with burnup. As the oxide layer grows, the compressive stress at the outer layer of oxide is not sustained and consequently the tetragonal phase becomes unstable and transforms into the monoclinic part. Such a change causes the formation of a nice interconnected porosity within the oxide movie which allows the oxidizing water to return in contact with the metal surface.
Cladding is an outer layer of either vertical or horizontal materials, used to improve the looks, thermal insulation and the climate resistance of a building. Our cladding is on the market in quite a lot of sizes, kinds of timber and floor finishes. Enhance the curb appeal of your house with B&Q cladding. All of our timber is responsibly sourced forest friendly timber. Once the pellet/clad hole is closed, any change in pellet dimensions causes stress in the cladding and the synergy between the stress and the corroding medium induces the SCC process.
Standard Zry is sufficiently exhausting to be susceptible to emphasize-corrosion cracking (SCC) when the pellet–cladding gap closes and the swelling fuel generates substantial tensile hoop stresses in the cladding. In the presence of an aggressive fission product (iodine is most often cited), a brittle crack can be initiated and penetrate the cladding wall. This is a primary cladding failure that admits steam into the rod with the accompanying potential for a more serious secondary failure due to hydriding. The mixture of circumstances (prone metallic, tensile stress, and chemical enhancer) that produces the primary defect is termed pellet–cladding interplay (PCI). The authentic objective of tin in Zry was to mitigate the loss of corrosion resistance brought on by pickup of impurity nitrogen during fabrication of the alloy.
These frameworks have been applied and peer reviewed throughout the scope of fireside analysis studies on the fire performance of aluminium composite panels and insulation materials at The University of Queensland and the University of Edinburgh. This giant scale test, undertaken by the Fire Protection Association (FPA), tested a HPL panel system with stone wool insulation, in accordance with British Standard 8414. This test includes building a 9-metre high wall with an entire cladding system fixed to it - including panels and insulation. This was then subjected to a hearth designed to replicate the circumstances by which a severe fire breaks out of a window.
Cladco’s cladding solutions are also moisture resistant, bettering their longevity and minimising the regular upkeep required for other cladding choices. The flammability of cladding supplies (aluminium composite panels, insulation, and some other supplies corresponding to sarking) is outlined based on nicely-established testing frameworks broadly accepted in the fire security engineering neighborhood.
In addition to metallurgical elements, water chemistry has a strong influence on the corrosion process in zirconium alloys. The control of water chemistry as required in several reactor systems embody appropriate additions of lithium hydroxide, boric acid, hydrogen/deuterium, oxygen, iron, and zinc. In PWRs, boric acid is added to the coolant water for reactivity management. The pH of the coolant is adjusted by addition of lithium hydroxide which renders the coolant slightly alkaline, so as to scale back the corrosion charges of structural materials (stainless steels and Inconels) within the main warmth transport circuit and thereby inhibit deposition of corrosion products on the gas cladding. Radiolysis of water produces oxidizing species which reinforces oxidation price of zirconium alloys in the radiation environment .
The blades had a machined pocket, into which powdered cobalt-primarily based metallic (Stellite 6) was fed forward of the laser beam. The ensuing cladding layer was nicely bonded, and the blades exhibited improved fatigue characteristics compared with blades shaped by the standard silver brazing process.
After melting and bonding by the laser, the alloy layer was 1.5 mm thick and had very little dilution from the metal. The resulting surface had glorious put on resistance. Architectural steel cladding is the collective term for exterior building cladding produced from coated steel. In the final a long time steel turned one of the most in style building supplies for the constructing envelope among architects and builders.
With the development of an equilibrium pore and crack structure in the oxide layer, the oxidation price successfully turns into linear, a attribute feature of the post-transition oxidation habits. Alloying elements, particularly tin, niobium, and iron, current within the α-stable answer strongly influence each the kinetics and the mechanism of oxide development in zirconium alloys. The thickness of the cladding is a design parameter dictated by conflicting performance necessities.
In order to prevent or minimize pellet/clad interactions, each mechanical and chemical, a coating of graphite powder is applied on the inside floor of cladding tubes. The graphite layer offers lubrication to reduce the mechanical interactions, and acts as a barrier towards the migration of harmful species to careworn regions of gasoline tubes. Laser cladding normally includes overlaying a relatively cheap substrate material with a costlier alloy that will increase the resistance of the half to wear or corrosion. Cladding allows the bulk of the half to be made with inexpensive materials, while offering the floor with desirable properties related to the dearer cladding materials.
tube. Energy, from fission, is generated roughly uniformly throughout the gasoline pellets. Heat is extracted at the rod surface by the coolant circulate. The temperature at the hottest point, on the pellet centerline, is often within the vary 800–a thousand °C, relying on the ability degree. The metallic cladding is an efficient conductor, so the temperature rise across the wall is just a few tens of degrees.